Events and Meetings
News
Harwick Standard adds Neville Chemical to Supplier Portfolio
Harwick Standard adds Neville Chemical to Supplier Portfolio Details
Akron, OH (September 3, 2024) - Harwick Standard Distribution Corporation, headquartered in Akron, Ohio, is pleased to announce their appointment as the distributor for USA and Canada for Neville Chemical, headquartered in Pittsburgh, Pennsylvania, effective October 1, 2024. This relationship will enable Harwick to market products further into the rubber, plastics and other polymer related market segments.
Neville Chemical is a leading manufacturer of low molecular weight thermoplastic and liquid resins that serve a wide variety of applications in the Coatings, Adhesives, Ink and Rubber Industries. Customer satisfaction, innovation, and extensive research have been hallmarks for nearly 100 years.
In 1948, Neville Chemical introduced its first petroleum hydrocarbon resin that not only exhibited excellent formulation properties.
Today, Neville Chemical Company is one of the world’s most highly respected hydrocarbon resin producers, known for its innovative research, high quality products, exceptional customer service, and competitive pricing. Its products enhance the performance characteristics of manufactured goods such as coatings, adhesives, ink, roofing, and rubber.
Harwick Standard has serviced the rubber, thermoplastics and other polymer-related industries for more than 90 years. Harwick Standard is a management owned and operated sales, marketing and technical support organization headquartered in Akron, Ohio. In addition to its corporate offices and warehouse facility in Akron, Harwick has a second office and warehouse facility located in Pico Rivera, CA, and has developed a logistics network across the country.
Harwick Standard is a proud member of the Alliance for Chemical Distribution (ACD). With its highly-skilled and experienced sales force, and top-rated customer service department, combined with supplying world-class quality products, Harwick sets the standard in service and reliability.
Information on the Company’s products and services can be found on their website at
www.harwickstandard.com.
Media Contact
Mr. William Knezevich
Harwick Standard Distribution Corporation
(330) 798-9300
Mr. Matthew Brown
Neville Chemical Company
(412) 335-2011
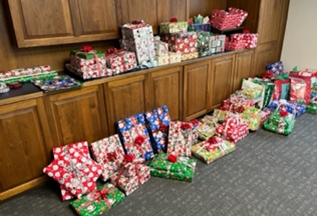
Harwick Standard, Western Reserve support Education Alternatives' Giving Tree
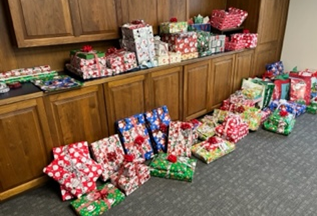
Harwick Standard, Western Reserve support Education Alternatives' Giving Tree Details
Harwick and Western Reserve employees supported Education Alternatives’ Giving Tree, providing many items on their students “Christmas Wish Lists.” Harwick President, Ernie Pouttu, noted we have been doing this giving tree for a number of years. The gratefulness of the students and the joy of particularly the younger ones is heartwarming.
Education Alternatives (EA) is a non-profit private school, with over 20 years’ experience educating special education students. EA offers school-day programs for students with social-emotional, behavioral and autism spectrum issues.
EA works with families and school districts to provide education services, based upon the students Individualized Education Program, for children who are struggling in their public or charter school. Each EA program is staffed by licensed teachers and mental health support staff. EA provides services in eight locations in Northeast Ohio.
Harwick Standard is a management-owned and operated technical, sales and marketing organization headquartered in Akron, Ohio, servicing the rubber, thermoplastics and other polymer-related industries for 90 years,. The ISO 9001 registered company operates a nationwide distribution network, supplying world-class products since 1932.
www.harwick.com
www.easchools.org
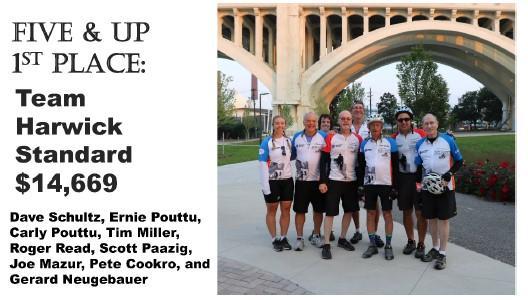
Five & Up 1st Place: Team Harwick Standard
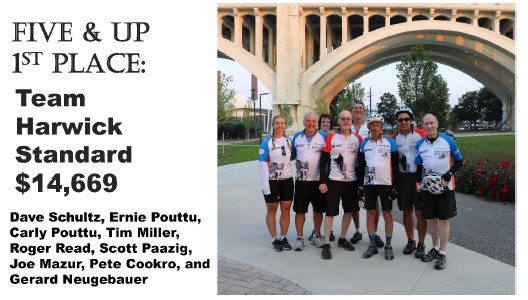
Five & Up 1st Place: Team Harwick Standard Details
FOR IMMEDIATE RELEASE: Harwick Standard Distribution Corporation
A first place finish for a first class team!
Their legs were pumping and their hearts were pounding over 101 long miles as they conquered the entire Ohio & Erie Canal Towpath Trail — peddling from Cleveland to New Philadelphia — in a single
day. They also conquered an entire category of riders, as Team Harwick Standard was awarded 1st place in the 2022 Huntington Towpath Century Ride fundraiser for groups of five and up.
Better still, they raised $14,669 to help benefit the continued development, maintenance, and enhancement of the Ohio & Erie Canal Towpath Trail. Eight hardy souls made up Team Harwick
Standard and embarked on this September adventure: Harwick retirees Roger Read and Dave Schultz (now with Rubber World); Scott Paazig from Cooper Standard; Gerard Neugebauer, Mayor of Green; Tim Miller, Joe Mazur, Pete Cookro, Carly Pouttu; and Ernie Pouttu, President of Harwick Standard.
While Harwick Standard has serviced the rubber, thermoplastics and polymer-related industries for 90 years, they have also participated in all 13 annual Towpath Century Rides dating back to 2010. Given their success whipping up donations and whipping down the trail, it is certain they will continue to participate in this event.
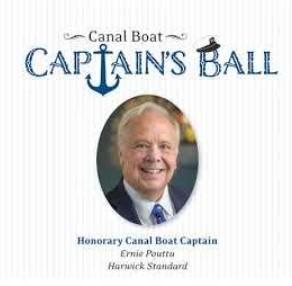
Ohio & Erie Canalway Coalition selected Ernie as the 2022 Canal Boat Captain
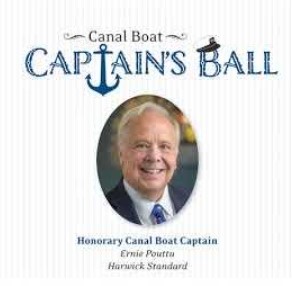
Ohio & Erie Canalway Coalition selected Ernie as the 2022 Canal Boat Captain Details
As you may know, Ernie Pouttu is involved in many community organizations, and supports various events.
This year, the Ohio & Erie Canalway Coalition selected Ernie as the 2022 Canal Boat Captain.
Attached is a video link honoring Ernie for his continuous efforts over the years. This video is a testament to his passion and enthusiasm for supporting community action.
Ohio & Erie Canalway Coalition video link
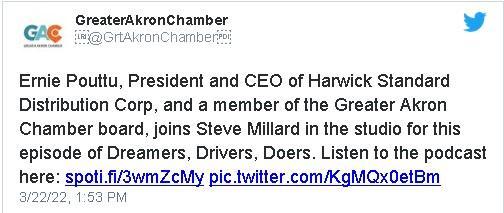
Dreamers, Drivers, Doers Podcast with Ernie Pouttu
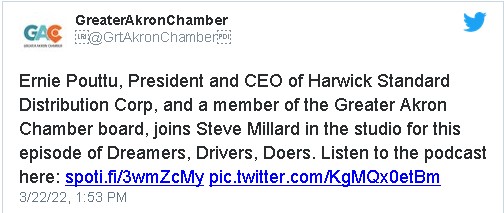
Dreamers, Drivers, Doers Podcast with Ernie Pouttu Details
The link below will take you to the recent Tweeted podcast between Ernie, and Steve Millard of the Greater Akron Chamber. It’s part of the Dreamers, Drivers and Doers segment conducted by the GAC. It’s worth listening to!
Ernie answers a lot of questions and covers a number of different topics. He talks about what brought him to the Akron area, how he got his start with Harwick, some of the boards he serves on, different organizations he volunteers for, and specific events he likes to support.
Spotify Podcast Dreamers, Drivers, Doers
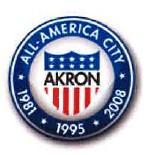
Akron Bicentennial Commission
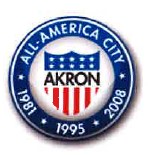
Akron Bicentennial Commission Details
In January 2022 Akron Mayor Dan Horrigan announced that planning is underway for the City's 200th Birthday in 2025. The Akron Bicentennial Commission, a myoral advisory board, has been established to oversee the planning and programming surrounding Akron's Bicentennial celebration. The Citizen-led initiative will eventually have representatives from neighborhoods, special interest groups and every ward in the city.
On December 6, 1825 General Simon Perkins file the plat of Akron at the courthouse in Ravenna. Akron's 200th year begins Decemer 6, 2024, and in line with prior commemorations of city anniversaries (1925, 1975, 2000), the Akron Bicentennial Celebration is scheduled to take place in July, 2025.. Special events would also mark Dec. 6, 2025, Akron actual 200th anniversary.
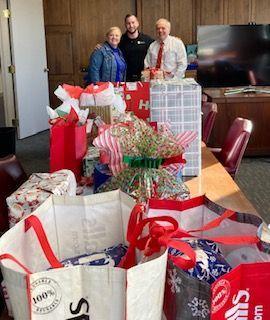
Harwick Standard supports Education Alternatives Giving Tree
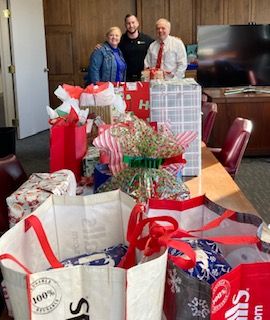
Harwick Standard supports Education Alternatives Giving Tree Details
The employees of Harwick Standard were able to put smiles on the faces of many students this Christmas season.
Harwick employees supported Education Alternatives’ Giving Tree, providing many items on their students “Christmas Wish Lists.”
Education Alternatives (EA) is a non-profit private school, with over 20 years’ experience educating special education students. EA offers school-day programs for students with social-emotional, behavioral and autism spectrum issues.
EA works with families and school districts to provide individualized education services, based upon the students Individualized Education Program, for children who are struggling in their public or charter school. Each EA program is staffed by licensed teachers and mental health support staff. EA provides services in eight locations in Northeast Ohio.
Harwick Standard is a management-owned and operated technical, sales and marketing organization headquartered in Akron, Ohio, servicing the rubber, thermoplastics and other polymer-related industries for more than 85 years,. The ISO 9001 registered company operates a nationwide distribution network, supplying world-class products since 1932.
www.harwick.com
www.easchools.org
12/15/2021
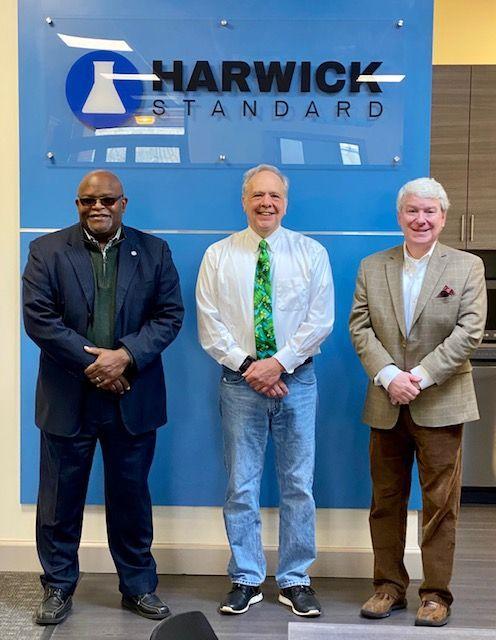
Harwick Standard President & CEO, Ernie Pouttu welcomes...
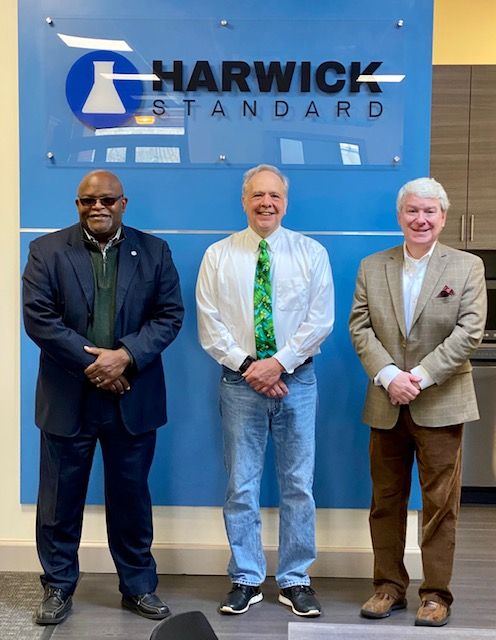
Harwick Standard President & CEO, Ernie Pouttu welcomes... Details
Harwick Standard President & CEO, Ernie Pouttu welcomes a visit from Sam DeShazior, City of Akron, Deputy Mayor, Economic Development and Gregg Cramer, Greater Akron Chamber, Vice President, Economic Development
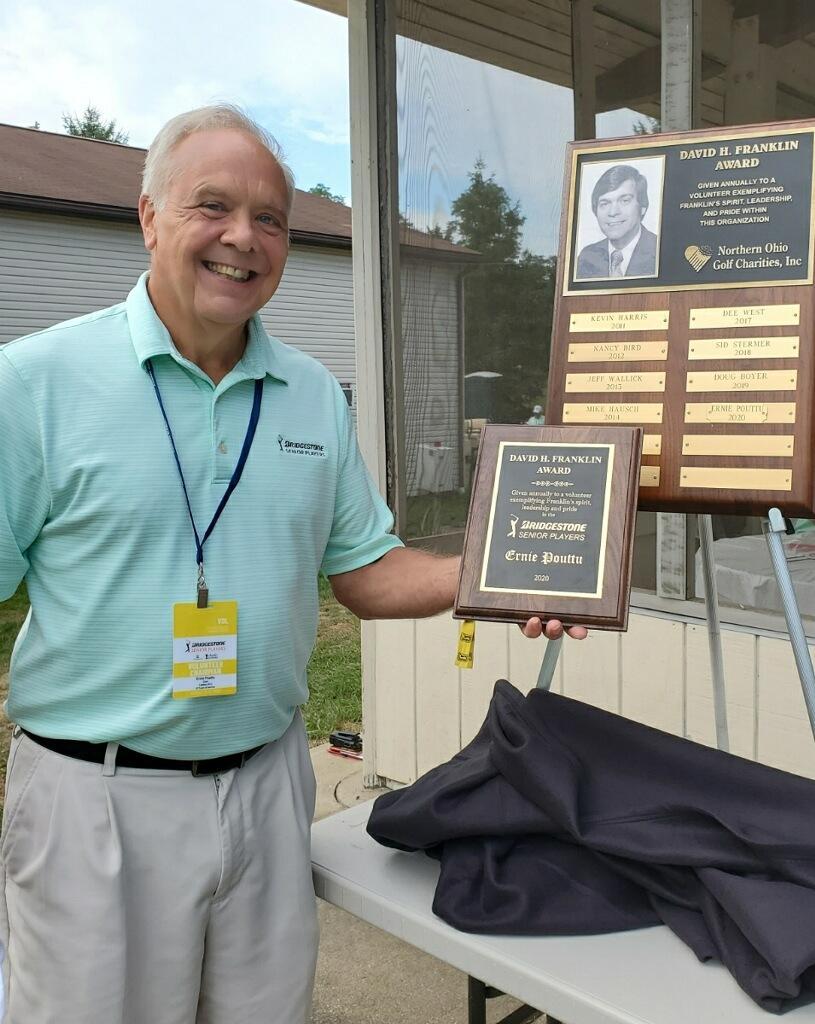
Harwick Standard CEO receives David H. Franklin Award
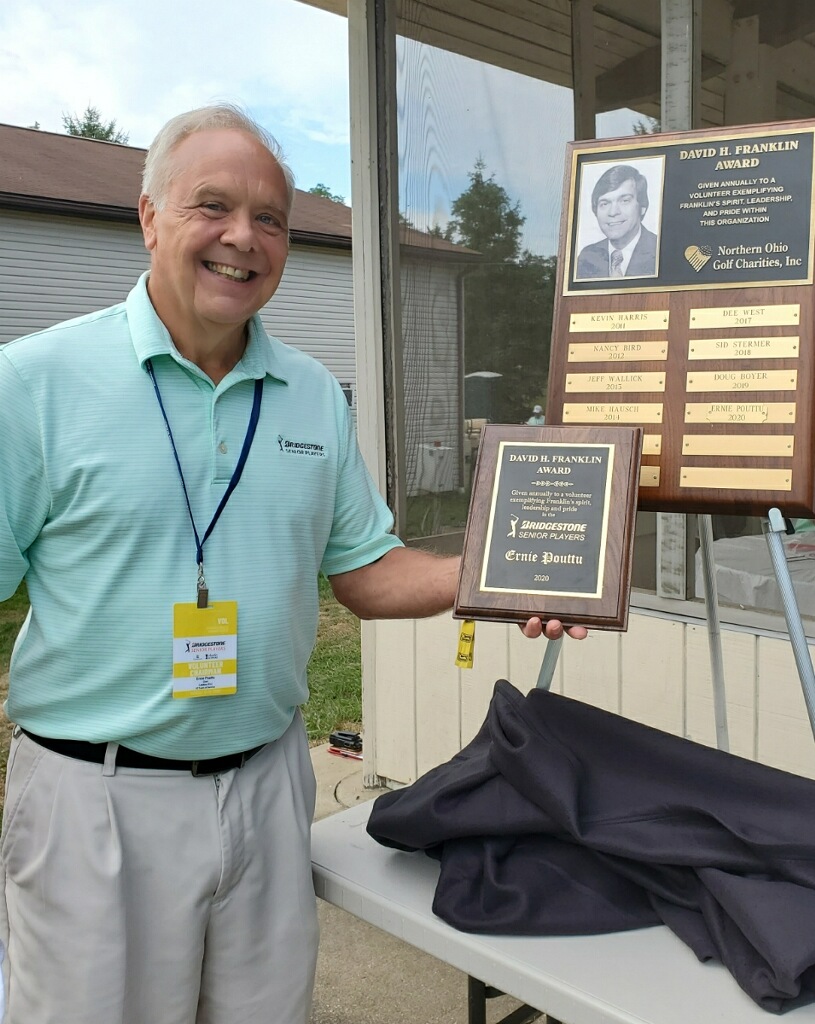
Harwick Standard CEO receives David H. Franklin Award Details
For more than six decades, thousands of dedicated volunteers have helped run successful professional golf tournaments at Firestone Country Club. Each year during the tournament, our volunteers are asked to nominate someone from their ranks who exemplifies the true and selfless meaning of being a volunteer. This highly respected award is named for David H. Franklin, a long-time volunteer who worked at the tournament for 25 years before losing his battle with cancer. The award recipient is announced at the Volunteer Breakfast held on Saturday of tournament week.
As the tournament draws to a close, a committee selects a recipient from those nominated based on the following criteria:
- Volunteer with Northern Ohio Golf Charities, Inc. for five years
- Personal dedication and commitment to making the tournament a success
- Positive response, regardless of how mundane the required task
- Unselfish in her/his efforts, focused on the tournament success and the impact on the community.
Congratulations Ernie Pouttu on your David H. Franklin Award!
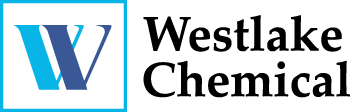
Westlake Chemical - EPOLENE® polymers
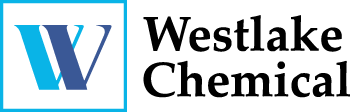
Westlake Chemical - EPOLENE® polymers Details
In EPDM compounding applications, oils are frequently used as a processing aid to improve mixing and processability. Independent laboratory studies have recently shown that the addition of EPOLENE® low molecular weight polymers can enhance mold fill performance and processability without loss of physical properties. The data generated by these studies show that just a 5 phr of EPOLENE® N-14 added to the compounding:
- Enhanced mold fill performance over control, comparable to increased oil loading of 10 phr
- Bolstered overall physical properties of the molded article vs. increasing oil levels
- Improved scorch time of the compounds vs control
http://www.harwick.com/files/WLK-EpoleneRubberCompounding.pdf